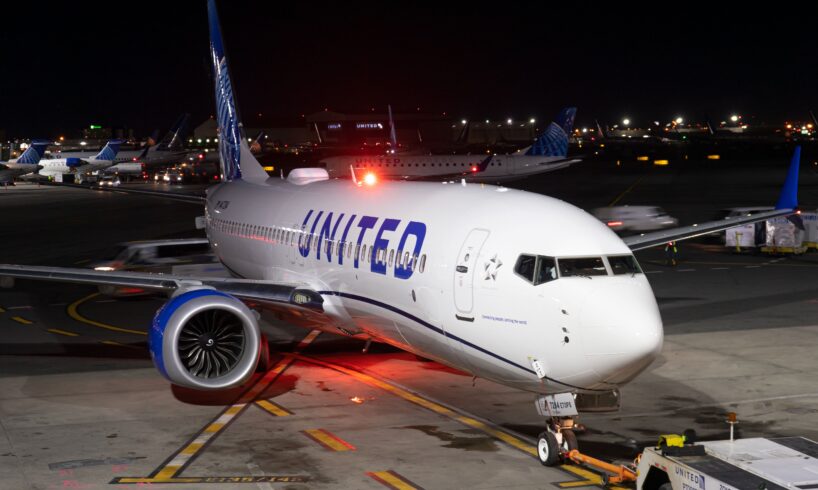
After two crashes involving the Boeing 737 Max
, which were fatal for all passengers and crew onboard, the aircraft earned a great deal of criticism. The crashes and subsequent exposure of their underlying causes resulted in public trust in the Boeing brand being diminished. It turned out that many of the issues with the plane stem back to the engine that was chosen for the plane, which was so large that it required unorthodox positioning on the aircraft.
Boeing
Stock Code
BA
CEO
Kelly Ortberg
Headquarters Location
Chicago, USA
The engine used by the 737 MAX is the CFM International LEAP high-bypass turbofan engine, which was produced by CFM International, a 50–50 joint venture between GE Aerospace and Safran Aircraft Engines, a French manufacturer. The engine itself is fairly well regarded, and is used successfully on other aircraft, such as the COMAC C919 and the Airbus A320neo
, with the latter being the direct competitor of the 737 MAX.
The competition with the A320neo was another factor that led to the flaws seen with the 737 MAX. However, as this article will expand upon, the fault in the case of the fatal 737 MAX crashes lies not with CFM International, but with Boeing and the choices made during the aircraft’s development.
Why Are Aircraft Engines Getting Larger?
As shown in the video above, courtesy of Popular Mechanics, increasing the size of a turbofan engine can increase its efficiency up to a point. The comparison of jet fighter engines to passenger turbofan engines is a good one, as it aptly shows over 70 years of jet propulsion development with one quick example:
Fighter jets must be small and high-performance, decreasing the likelihood of detection and presenting a smaller and more elusive target for enemy weapons. Thanks to aircraft carriers, they can be launched at a short distance from the target, eliminating the biggest downside of jet engines: lower fuel efficiency.
Passenger aircraft must be efficient, traveling the furthest possible distance on the lowest amount of fuel, and in a reasonable amount of time. Increased range means increased utility and more destinations it is possible to reach. As shown with the demise of Concorde, efficiency is more important than speed.
The optimal engine type for efficient passenger aircraft flight is the turbofan. Large modern turbofans are often referred to as being ‘high-bypass’ engines, which means that a large amount of air is pushed through the engine via the fans, ‘bypassing’ the jet component of the engine. A comparatively small amount of air passes into the jet component and is ignited with the fuel.
It turns out that the most optimal engine size, balancing performance and fuel efficiency against the increased wind resistance due to overall engine size, is a little over 13 feet. Therefore, during the development of the 737 MAX, the desire would have been strong to mount large engines on the aircraft, allowing it to meet desired performance, fuel efficiency, and environmental targets.
The LEAP Engine & Airbus Competition
Photo: Safran Group
The 737 MAX was intended to be the successor to the 737 NG, and is the fourth generation of the Boeing 737 family of commercial planes. Though manufacture began in 2014, the first delivery of the aircraft was in May 2017 to Malindo Air. Boeing was intent on catching up with its largest competitor, Airbus, which had begun manufacturing its new narrowbody airliner, the A320neo, in 2012. The A320neo began deliveries in 2014, a few years ahead of Boeing with its equivalent plane.
Equivalent 737 MAX and A320neo aircraft compared
Boeing 737 MAX 8
Airbus A320neo
Seats (2-class configuration)
178
165
Cargo Capacity
1,540 cu ft
1,300 cu ft
Range
3,500 NM (6,500 km)
3,500 NM (6,500 km)
Cruising speed
Mach 0.79 (453 kn; 839 km/h)
Mach 0.78 (450 kn; 833 km/h)
Ceiling
41,000 ft
39,100–39,800 ft
Length
129 ft 6 in
123 ft 3 in
Wingspan
117 ft 10 in
117 ft 5 in
Max Takeoff Weight (MTOW)
182,200 lb
174,200 lb
Fuel Capacity
6,820 US gal
7,835 US gal
Engine
2x CFM International LEAP-1B
2x CFM International LEAP-1A
-or-
2x Pratt & Whitney PW1100G
The A320neo has great emphasis on the revolutionary modern turbofan engines that it is available with. Indeed, ‘neo’ stands for New Engine Option, and it began deliveries with the Pratt & Whitney PW1100G-JM engines, with plans to also accommodate the CFM International LEAP-1A engines. Of course, the latter is the same type that the 737 MAX would eventually use.
Both engines are high-bypass turbofans, which offer greater efficiency than previous generations of engines. According to the Safran Group, the LEAP offers a 15% reduction in fuel consumption and CO2 emissions compared to previous-generation engines, with a reduction of up to 50% reduction in NOx emissions in accordance with the ICAO’s CAEP/6 environmental standard. For Boeing, these were very desirable stats to be able to attach to its next generation of 737s.
Related
Why The Boeing 737 MAX Has Taller Landing Gear Struts
It is approximately six inches taller than its predecessor.
How Boeing Accommodated The Engine
Photo: Artur Buibarov | Shutterstock
Boeing found itself in a situation where it was at risk of being left behind by Airbus. The A320 and 737 had largely been comparable up until that point, and airlines were beginning to put pressure on Boeing to produce a competitor. One option Boeing had was to build a new narrowbody aircraft capable of accommodating the larger LEAP engines through a five-to-eight-year design and certification process. However, this would still be too late for most airlines’ immediate needs.
The other option was to modify the old, reliable 737 platform for the new engines, making adjustments for their increased size. Normally, a change like this would cause many differences to the aircraft’s dimensions. The larger engines would require higher-set wings, and consequential changes would include different facilities at airports and pilot training to adjust to the new 757’s handling characteristics. A new type certification would also be needed for the new 737 model to fly.
Instead of biting the bullet and doing this, Boeing opted to use the same 737 NG airframe, mount the larger engines forward and upwards of their optimal position, and lengthen the landing gear struts. Boeing also added a new software system called the Maneuvering Characteristics Augmentation System (MCAS) to compensate for the altered flight characteristics. Doing so eliminated the need for pilot training, but unfortunately, it was implicated as being responsible for the two fatal 737 MAX crashes.
Related
Boeing Settles To Avoid Civil Trial On 2019 Ethiopian Airlines Boeing 737 MAX Crash
Boeing was supposed to face a civil trial but reached a last-minute settlement.
The Danger Posed By The MCAS System
Photo: ThomasLENNE | Shutterstock
As a result of the Lion Air flight 610 crash on October 29th, 2018, and the Ethiopian Airlines flight 302 crash on March 10th, 2019, a total of 346 people died. It is fair to say that these deaths happened as a result of the design choices made for 737 MAX, as the MCAS system included an anti-stall measure that overrode pilot commands and has been found to have caused both crashes.
In these cases, the automated system forced the nose of the plane down after erroneous data from an external sensor prompted the system to move the tailplane, as examined at the Harvard Legal Forum of Corporate Governance. This may have been an effort to prevent pilot-induced oscillation, which caused the crash of a Bell 525 Relentless helicopter. In any case, automated systems come with their own dangers, and should never override deliberate pilot input.
Boeing has since been dragged through court cases regarding the crashes. Investigations into these accidents, as a result of whistleblowers coming forward, have exposed other problems and dangerous cost-saving measures at the company, revealing an unsafe culture in the manufacturing arm of the company. Boeing has been paying for their decision since, and even had to begin a $5 billion pilot retraining measure for use of the 737 MAX, according to Bloomberg.
Related
Boeing 737 MAX Fraud Trial Set For June 23rd
Boeing is in continued discussion with the DOJ regarding this case.
Examining The Advantages Of Low-Riding Aircraft
Photo: Rudzenka | Shutterstock
There are several practical advantages to the 737 MAX being low to the ground, especially when it comes to airport operations. In the case of the 737 MAX, the lower engines have become the aircraft’s hallmark, the flat-bottomed engines being likened to ‘hamster pouches,’ according to AN Aviation Services. The advantages of such a design include the likes of:
Easier Ground Handling: The low height simplifies the process of loading and unloading baggage, cargo, and passengers. Smaller airports with limited ground equipment need not invest in specialized high vehicles to accommodate the plane.
Faster Turnaround Times: As a result of easy ground handling, the 737 MAX can be turned around quickly between flights. For short-haul routes with tight schedules, this is advantageous for airlines, as it reduces the likelihood of delays for the passenger.
Cost Efficiency: For airlines using the 737 MAX, the cross-compatibility of maintenance equipment and vehicles reduces complexity in a maintenance schedule. Simpler is better, and introduces fewer points of failure.
However, there are a few downsides, as the lower engines are more likely to suck up debris from the ground. The clearance also makes the aircraft challenging to operate on rough or uneven runways.
Overall, as 1,784 examples of 737 MAX aircraft have been built as of March 2025, the 737 MAX has perhaps proved itself to be capable. The crashes represented a pair of black marks against its name, but, with the New York Times reporting that the FAA is auditing Boeing as a result of the aircraft’s issues, it is possible that the company’s problems are on the way to being resolved.